For people working with aluminum parts, it is quite noticeable that some parts have this distinct glow or surface attributes which makes them better in terms of quality, function, and aesthetics. This is possible by using a process called anodizing.
Anodizing is a popular custom sheet metal surface finishing process in manufacturing because of the attributes it confers on metals, of which aluminum is a common one. We’ll be going into depth about anodizing, its types and why aluminum parts need anodizing. We’ll also highlight some top tips that could help you when anodizing aluminum parts.
What is Anodizing?
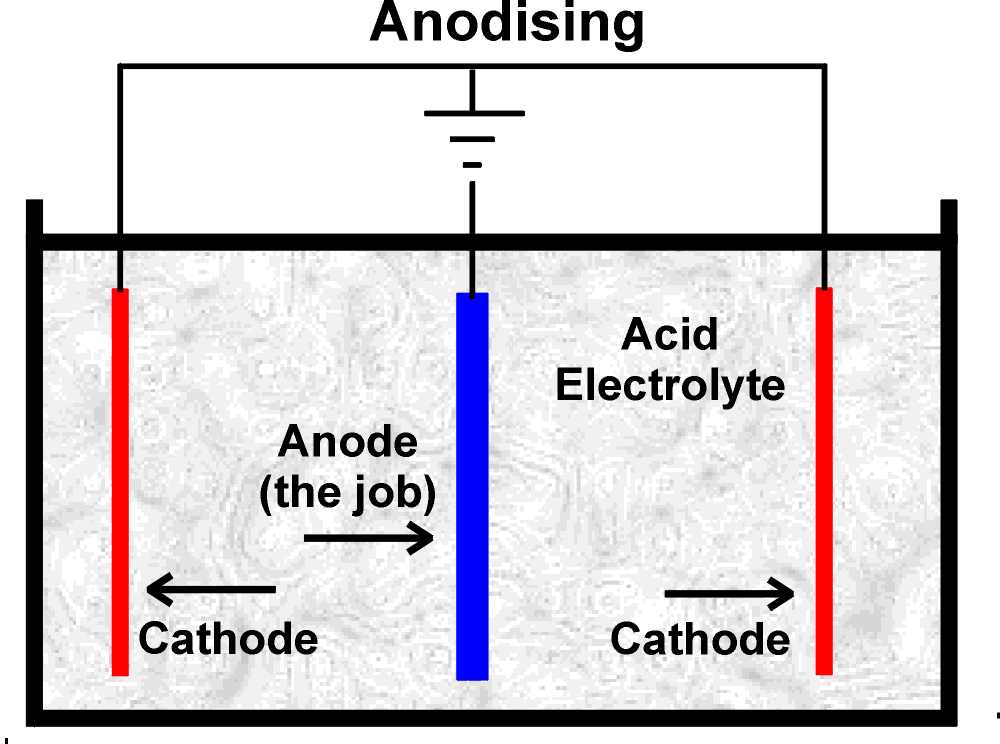
Anodizing is a surface finishing process that involves electrochemically forming an oxide film on a metal such as aluminum. It is a popular surface finishing process for aluminum parts. However, the procedure is also suitable for other metals such as magnesium and titanium.
Types of Anodizing Process?
There are three types of anodizing processes you could use for aluminum parts. Each one has varying properties as a result of the different electrodes, electrolytes, and power used.
Type 1 Anodizing Process:
Also known as the Light Anodizing process involves putting the aluminum part in a container containing chromic acid as the electrolyte. The aluminum part is the anode. On passing a current through the electrolyte, particles of aluminum leave the part’s surface to form microscopic grooves. On oxidizing, it forms an oxide layer that has better heat and is corrosion-resistant when you compare it with pure aluminum.
Type 2 Anodizing Process:
The type 2 anodizing process is similar to type 1. However, unlike type 1, the electrolyte is sulfuric acid. Due to the higher potency of the electrolyte, it forms a deeper groove and thicker oxide. Since the grooves are deeper, when you use type 2 anodizing, there is better paint retention.
Type 3 Anodizing Process:
Also called hard anodizing, this process is similar to type 2. However, unlike type 2, a higher voltage is used. The type 3 anodizing process is suitable for making heavy wear parts.
Reasons Why Aluminum Parts Need Anodizing
Anodizing boasts of many advantages among other surface finishing processes used in custom sheet metal fabrication. Below is the attribute it impacts on the aluminum part, which necessitates why you should choose the technique.
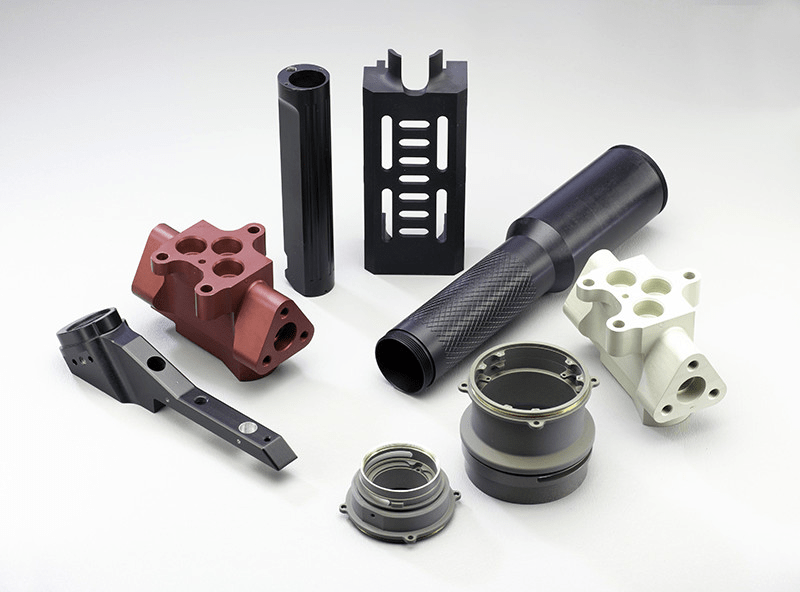
1. Corrosion-Resistance
On anodizing the aluminum parts, the surface becomes corrosion resistant. This property is a result of the stabilization of the surface due to the formation of the oxide coating. At high or low temperatures, the oxide is unreactive and strong (although the type of anodizing you use plays a huge role in its strength). Due to the corrosion resistance properties, anodized aluminum parts are resistant to many chemical reactions and are suitable for different operations.
2. Decoration
Anodized aluminum parts have better aesthetic properties. You can also have color finishing with aluminum parts. For example, anodizing colors include black, blue, gold, grey, red, etc. This makes it a popular surface finishing process for those who value and want a beautiful and unique finish on their aluminum products.
3. Durability/ Wear-Resistance
Anodized aluminum parts have a very hard surface due to the oxide formation and are harder than the base metal. The durability or wear-resistance property depends on the type of anodizing used, with type 3 anodized aluminum parts having the highest durability/wear resistance. When done, it can reach metal cutting tool steels.
4. Insulating Layer for Electricity
Anodized aluminum parts have insulating properties due to the oxide having lower electrical conductivity than un-anodized aluminum parts. Therefore, anodizing is suitable for making products used in such a capacity.
5. Base Layer for Painting
Anodizing leads to the formation of pores on the aluminum parts and the degree of pore size and depth depending on the type of anodizing process used. For aluminum parts that require painting not to peel off, anodizing is a suitable surface finishing process. Therefore, when used, peeling or other mechanical actions cannot result in scratching off of color.
6. Low Cost/High value
Anodizing increases the value of the aluminum parts while lowering the manufacturing cost. When you compare the service life of an anodized aluminum part to other surface finished base aluminum parts, you will see the difference in service life and how much was used to get such value.
7. Guaranteed Quality
Anodizing is a popular surface finishing process because of its high precision and quality-assuring procedure. Therefore, for those who value quality and use the best surface finishing practices, anodizing is the right surface finishing process to use.
Top Tips to Enhance Anodizing
Anodizing your aluminum parts might seem a complex process. However, it is not. Below are some tips that can help assure you of a quality finish when used.
1. Decide on Which Type to Use…
The type of anodizing process suitable for a process depends on the quality you desire and the type of aluminum parts or other metals that you are working with. For deep grooves and better paint retention, it is better to go for the type 3 anodizing process.
The chosen aluminum alloy must be the same as the one used with the incoming parts. This is important because different alloys require different surface finishing. Therefore, it is important to know your alloy.
2. Remove Oils & Fingerprints
The metal on which you want to perform the anodizing process must be free from all levels of contamination as this can lead to a problem with the finishing. Therefore, inspect and remove any form of contamination whether oils, debris, and fingerprints, to have better success rates.
3. Stay Current in the field
Anodizing is not a static process as further development occurs to improve production efficiency and effectiveness. Therefore, you must keep yourself abreast of changes occurring in the process.
Aluminum itself in an unfinished state is popular as a material used for its quality and aesthetic attributes. However, with the advent of anodizing, there came a chance to improve on such attributes. This article introduced anodizing, the types, and, more importantly, why aluminum parts need anodizing.